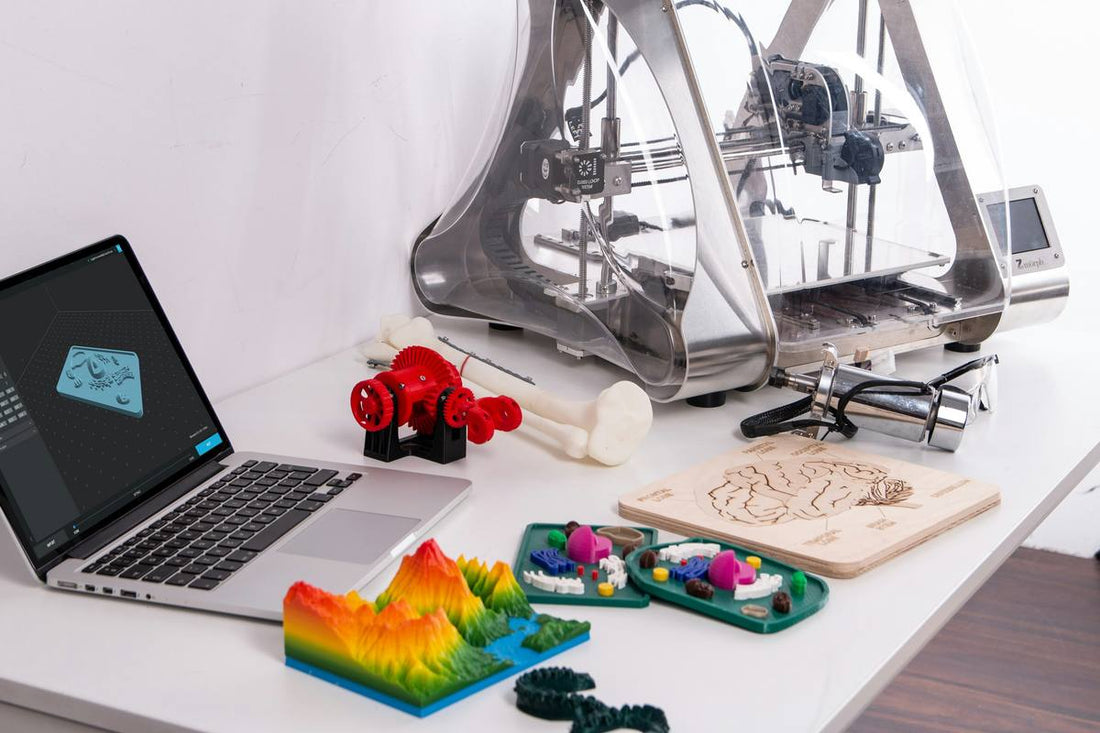
Additive Manufacturing Business
Additive manufacturing (AM), commonly known as 3D printing, has rapidly evolved into a viable business sector with diverse applications across industries. Additive manufacturing refers to a process where materials are added layer by layer to create objects from 3D model data, as opposed to traditional manufacturing methods, which often involve subtracting material through cutting, drilling, or milling. This technology allows for high levels of customization, rapid prototyping, and efficient production of complex geometries that would be difficult or impossible to achieve with conventional techniques.
The global additive manufacturing market has seen significant growth, driven by advancements in technology, materials, and increasing adoption across various industries. The market was valued at approximately $15.2 billion in 2023 and is expected to continue its expansion, reaching upwards of $50 billion by 2030. This is not a creditable number; however, the sharp increase is agreed across all resources.
Key trends driving this growth include:
- Advances in Materials: The development of new materials, including metals, composites, and biocompatible materials, has expanded the range of applications for additive manufacturing.
- Industry 4.0 Integration: Additive manufacturing is a critical component of Industry 4.0, allowing for digital twins, decentralized production, and enhanced supply chain flexibility.
- Sustainability Focus: AM enables more efficient use of materials, reducing waste, and can often result in lighter, more efficient designs that lower energy consumption in the end-use phase.
Business Models in Additive Manufacturing shown in Figure 1.
Figure 1: Additive Manufacturer Business Models.
End users of the additive manufacturing industry span across various sectors, including aerospace, where companies use AM for lightweight, complex components; healthcare, where it is employed for customized implants, prosthetics, and tissue engineering; automotive, for rapid prototyping and specialized parts; consumer goods, particularly for customizable products like fashion, footwear, and electronics; and manufacturing industries that require rapid prototyping, tooling, and on-demand production of specialized parts. Additionally, sectors like architecture, education, and even food production are increasingly adopting AM technologies for their unique needs.
Challenges in Additive Manufacturing mainly are:
- High Initial Costs: Although costs have decreased, the initial investment in AM technology can still be significant.
- Regulatory Hurdles: In regulated industries like aerospace and healthcare, gaining certification for additive-manufactured parts can be complex and time-consuming.
- Material Limitations: While the range of materials is expanding, certain applications still face limitations in terms of material properties, such as strength, durability, and heat resistance.
- Intellectual Property: The ease of copying digital designs presents challenges related to IP protection and counterfeit products.
Additive Manufacturing Business Models
In AM, there are multiple routs that can be chosen in the industry that can go through various understanding and information. The list is generally discussed below:
Service Bureaus offer on-demand 3D printing services to clients who do not have in-house AM capabilities. They cater to a wide range of industries, providing prototyping, short-run production, and custom manufacturing. This model is popular with startups, small businesses, and even large companies that need specialized or overflow capacity.
Original Equipment Manufacturers (OEMs) are companies that design, produce, and sell their own AM machines. These businesses invest heavily in research and development to advance the technology, making their machines more precise, faster, and capable of working with a broader range of materials.
Hybrid Manufacturers integrate AM technology into their traditional manufacturing processes, using it to complement or enhance existing production methods. For example, a company might use AM to create complex tooling or molds that would be difficult to produce through conventional methods.
Material Suppliers focus on the production and distribution of the raw materials used in additive manufacturing, such as metal powders, polymers, ceramics, and composites. As the variety of materials available for AM grows, these companies play a crucial role in expanding the applications of AM across industries. Specialized Material Developers work on creating custom materials with unique properties tailored to specific industry needs, such as biocompatibility for medical devices or heat resistance for aerospace components.
Software Developers create specialized design software that optimizes products for additive manufacturing. These tools often include features like topology optimization, generative design, and simulation, which help engineers create parts that are lightweight, strong, and material-efficient.
Consulting Services offer expertise in AM, helping companies integrate the technology into their operations, navigate regulatory requirements, and optimize their designs for AM.
Revenue Streams in Additive Manufacturing
Revenue from selling 3D printers, both industrial-grade and consumer-level, is a major income stream. This includes not only the initial sale but also ongoing maintenance, upgrades, and consumables. Selling the raw materials required for AM processes is another significant revenue source. The ongoing demand for these materials as AM becomes more integrated into production lines ensures a steady revenue stream.
Many companies generate revenue by providing printing services on a contract basis, often for companies that require rapid prototyping or short production runs. Service contracts also include maintenance and technical support for companies using AM machines.
Revenue from the sale of specialized design and manufacturing software & Services tailored for AM processes. This includes subscription models for ongoing use and support. Offering consulting services for companies looking to implement AM technology and providing training for their staff on how to operate and optimize the use of AM equipment.
AM is increasingly being used for on-demand production of spare parts and aftermarket components, especially in industries where maintaining large inventories of spare parts is costly or impractical.
Competitive Landscape
The AM industry is highly competitive, with players ranging from large, established companies to innovative startups. Companies that consistently push the boundaries of what is possible with AM, whether through faster printing speeds, higher precision, or the ability to use a broader range of materials, often have a competitive advantage.
The ability to work with a wide variety of materials, including metals, composites, and biocompatible materials, can set a company apart. Firms that develop proprietary materials with unique properties also have a strong competitive edge.
Some companies focus on specific industries, such as aerospace or healthcare, and tailor their products and services to meet the stringent requirements of these sectors. This is in which it sits the companies’ specialization.
Companies with a global presence can better serve multinational corporations and take advantage of opportunities in emerging markets where AM adoption is growing rapidly.
Managing Intellectual Property (IP) is crucial in the AM business, as the ease of replicating designs can lead to issues with counterfeiting and IP theft. Companies must invest in robust IP protection strategies. This is one of the strategic considerations required to be studied by the pioneer. Especially in industries like aerospace and healthcare, meeting regulatory standards is a significant hurdle. Companies must navigate complex certification processes to ensure their products meet the necessary safety and quality standards.
Integrating AM into traditional supply chains requires careful planning. Companies need to balance the benefits of localized, on-demand production with the logistical challenges it presents. As sustainability becomes increasingly important, companies in the AM space are exploring ways to make their processes eco-friendlier. This includes reducing material waste, using sustainable materials, and improving the energy efficiency of AM machines.
Figure 2: Additive Manufacturing Investments and Growth Opportunities.
As a new firm, Continued investment in research and development is essential for staying ahead in the AM industry. This includes developing new materials, enhancing machine capabilities, and refining software. A good base for Research and Development plan is required for this such field.
Forming strategic partnerships with companies in complementary industries, such as material science or software development, can accelerate innovation and market penetration. As AM technology becomes more accessible, there are significant opportunities in emerging markets where traditional manufacturing infrastructure is less developed. Companies can also explore new applications in fields like construction and food production.
Larger companies in the AM space may look to grow through acquisitions, buying up smaller firms with unique technologies or capabilities.