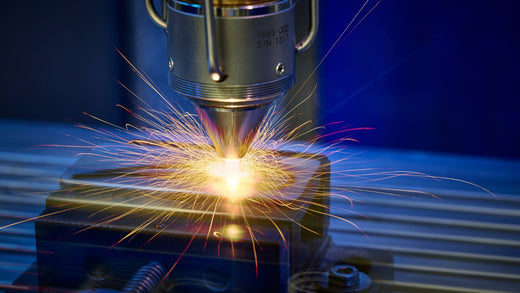
Additive Manufacturing In R&D Industry
Additive manufacturing (AM) has become a crucial tool in research industries, where its unique capabilities are leveraged to push the boundaries of scientific and technological innovation. Various research and technology required to be established and developed. The following research areas are discussed in detail that will widen the knowledge of 3D printing industry. The included areas are the major area, any other areas not mentioned considered to be minor and not recommended to be studied unless it’s a new field.
Material Science Research
Additive manufacturing enables researchers to experiment with novel materials that have unique properties, such as high-strength alloys, bio-compatible polymers, and composite materials. The ability to create intricate structures at a microscopic level allows for the development of materials with enhanced mechanical, thermal, and electrical properties. The ease to create multiple samples enhances the research capabilities to prove the theories/claims established.
Researchers use AM to produce small batches of materials for testing and analysis, which accelerates the process of material discovery and optimization. This approach is particularly valuable for testing new alloys, ceramics, and polymers under different conditions.
AM researchers can be specialized in certain industry in which requires material science research. Figure 1 below illustrate a glimpse of material science studies.
Figure 1: Additive Manufactured Samples Undergone in Electron Microscopes
Biomedical and Pharmaceutical Research
In biomedical research, AM is used to fabricate scaffolds for tissue engineering. These scaffolds can be customized to match the patient's anatomy and promote cell growth, leading to more effective regenerative treatments. Researchers are also exploring the potential of AM in printing entire organs, though this is still in its early stages. Additive manufacturing allows for the creation of custom drug delivery systems, such as 3D-printed pills that can release medication at controlled rates. This technology is also used to produce microfluidic devices, which are essential in drug testing and personalized medicine.
In the development of prosthetics and implants, AM enables the production of custom-designed components that fit the unique anatomical features of individual patients. This level of customization improves the effectiveness and comfort of medical devices. For example, an engineered based designer can custom-design plastic wrap used for broken bone recovery that is waterproof and comfortable for the patient.
Aerospace and Automotive Research
In aerospace and automotive research, AM is used to design and test lightweight structures that are optimized for strength and efficiency. By reducing the weight of components without compromising their integrity, researchers contribute to the development of more fuel-efficient vehicles and aircraft. Moreover, a smaller scale prototype can be designed to decrease that simulates the effectiveness of the tests. This will ensure a smaller cost for the research and reducing the time required to test.
AM allows for the rapid production of prototypes, which researchers can quickly test and iterate upon. This accelerates the development cycle for new aerospace and automotive technologies, such as advanced propulsion systems or aerodynamic components.
Researchers are exploring the potential of AM to reduce waste and energy consumption in manufacturing processes. Additive manufacturing enables precise material deposition, minimizing waste compared to traditional subtractive methods. Moreover, the capability to manufacture complex designs opens the door for the engineers to enhance aerodynamics requirements.
Environmental and Energy Research
AM is being used to create components for renewable energy systems, such as complex geometries for wind turbine blades or custom parts for solar panels. The technology also facilitates the development of new energy storage solutions, like advanced batteries and fuel cells. Additive manufacturing is utilized in the development of sensors and devices for environmental monitoring. These custom devices can be designed to detect specific pollutants or environmental changes, contributing to more effective environmental research and protection.
Academic Research and Education
Universities and research institutions use AM to explore new engineering designs and methodologies. The ability to create complex geometries and custom components enables researchers to test new theories and approaches in fields such as structural engineering, fluid dynamics, robotics, and sciences. Also, a powerful educational tool, providing students and researchers with hands-on experience in manufacturing and design. It allows for the creation of physical models that help in visualizing and understanding complex concepts in science and engineering.
AM fosters collaboration across disciplines, such as combining biology with engineering to develop bio-inspired designs or integrating chemistry with materials science to create new functional materials. This interdisciplinary approach often leads to breakthroughs that wouldn't be possible in isolated fields.
Researchers use AM to fabricate custom laboratory equipment and tools that are tailored to specific experimental needs. This includes everything from custom nozzles and reactors to specialized holders and fixtures. Moreover, tools that can be used in workshops can be easily fabricated which will enhance the experience the job in the workshop
In fields like nanotechnology and microelectronics, AM is used to create structures and components at a microscale or even nanoscale level. This capability is crucial for advancing research in areas such as semiconductor devices, sensors, and photonics.
In space exploration, AM is being researched for its potential to use local materials (such as lunar or Martian regolith) to create structures and tools on-site, reducing the need to transport materials from Earth. The ability to rapidly produce and test components for space missions is vital for innovation in space technology. AM allows researchers to design, test, and iterate spacecraft components with greater flexibility and speed.
Challenges in Additive Manufacturing in R&D Industries
There are multiple challenges that are still under consideration in AM capabilities. The following are the major constraints shown in Figure 2.
Figure 2: Additive Manufacturing Challenges in R&D Industry.
One of the ongoing challenges in using AM for research is ensuring that the material properties of 3D-printed components meet the required standards for specific applications, particularly in aerospace and biomedical fields. While AM is excellent for small-scale and intricate designs, scaling up these processes to larger sizes or maintaining high resolution in tiny components can be challenging.
The cost of high-end AM equipment and materials can be prohibitive for some research institutions, particularly those in developing regions. Accessibility to these technologies remains an issue that needs to be addressed.
Future Common Research Areas
As AM technology advances, it will continue to enable greater customization in research, allowing for the creation of highly specialized tools, materials, and components tailored to specific experiments and applications. This ensures a great integration to multiple industries.
The integration of AM with AI and machine learning could lead to smarter, more efficient design and manufacturing processes, where machines can optimize designs autonomously based on vast datasets. Such area can be used in all business models starting from services up to material suppliers.
As AM technology matures, it is likely to find applications in new research areas such as quantum computing, advanced biotechnology, and space colonization, driving innovation across multiple fields.