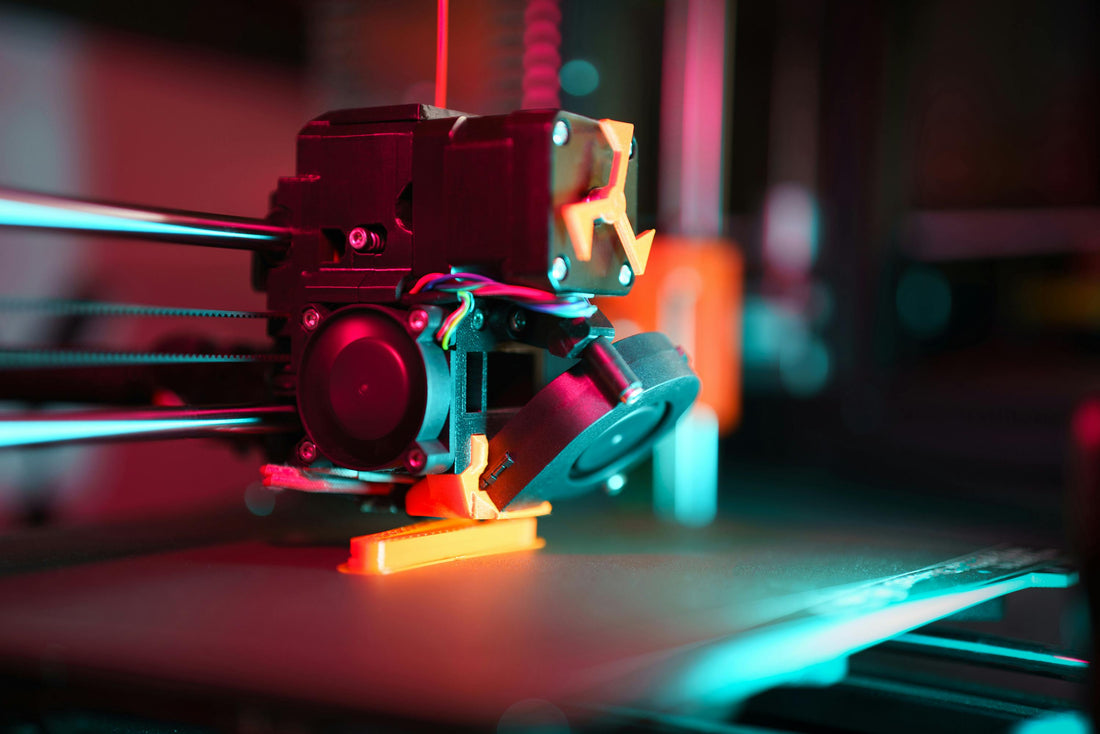
Additive Manufacturing Machine Types
In additive manufacturing, there are several technologies that utilizes the use various material to manufacture products layer by layer. The materials vary in different forms from plastics to resin to metals. Each technology has its pros, cons, costs, and durability.
The purpose of this document is to illustrate the differences between all the additive manufacturing machines that are available in the markets along with their uses in the industry. The Additive manufacturing machines that are available in the market are shown in the Figure 1 below.
Figure 1: Additive Manufacturing Machines
Stereolithography (SLA)
It works by a 3D printing technique called Vat Polymerization where a material called a photopolymer gum specifically restored by a light source. An SLA printer utilizes mirrors, called galvanometers. One is situated on the X-pivot, the other on the Y-hub. These point to the purpose of a laser pillar across the tank of gum, specifically relieving and setting a cross-part of the item in the forming zone, developing it layer by layer.
SLA is a quick prototyping measure where exactness and accuracy are taken seriously. It can create objects from 3D CAD information in only a couple of hours. This is a 3D printing measure its fine subtleties and precision by changing over fluid photopolymers (a unique kind of plastic) into strong 3D items, each layer in turn. The plastic is initially warmed to transform it into a semi-fluid structure, and afterward, it solidifies on contact. The printer develops every one of these layers utilizing a bright laser, coordinated by X and Y filtering mirrors. A recoater sharp edge also gets across the surface right before the next step to guarantee each thin layer of gum spreads equitably across the article. The print cycle proceeds thusly, building 3D items from the base up. When finished, the 3D part will typically have a synthetic shower to eliminate an overabundance. It’s additionally basic practice to post-fix the article in a bright broiler. This makes the product more grounded and steadier. A mechanism of the Machine diagram shown in Figure 2 below.
Figure 2: Stereolithography Additive Manufacturing Machine Diagram.
- How it works: SLA uses a laser to cure liquid resin into hardened plastic, layer by layer. The laser traces the object’s cross-section on the surface of the resin, solidifying it.
- Materials: Photopolymer resins with varying properties (e.g., rigid, flexible, durable).
- Applications: High-detail prototypes, dental models, jewelry.
- Pros: High resolution, smooth surface finish, fine details.
- Cons: More expensive, requires post-processing (e.g., washing, UV curing).
Selective Laser Sintering (SLS)
SLS parts are produced using genuine thermoplastic material, they are tough, reasonable for utilitarian testing, and can uphold living pivots and snap-fits. In contrast with SLA, parts are more grounded, yet have harsher surface completions. SLS doesn’t need help structures so the entire form stage can be used to settle various parts into a solitary form—making it appropriate for part amounts higher than other 3D printing measures.
A container of thermoplastic powder (Nylon 6, Nylon 11, Nylon 12) is warmed simply beneath its liquefying point. At that point, a recoating or wiper sharp edge stores a meager layer of the powder – generally 0.1 mm thick – onto the forming stage. A laser bar starts examining the surface, where it specifically ‘sinters’ the powder, which means it hardens a cross-part of the article. Likewise, with SLA, the laser is centered around an area by a couple of galvos. When the whole cross-segment is filtered, the stage drops somewhere near one thickness of layer stature and the entire cycle is rehashed until the item is completely made. Powder that isn’t sintered remaining parts set up supporting the item that has been sintered, dispensing with the requirement to support structures. Not many of the applications for SLS are the assembling of practical parts, complex ducting requiring empty plans, and low-run creation. Its qualities are in the production of utilitarian parts, which leaves behind great mechanical properties, and with complex calculations. A mechanism of the Machine diagram shown in Figure 3 below.
Figure 3: Selective Laser Sintering Additive Manufacturing Diagram.
- How it works: SLS uses a laser to sinter powdered material (usually nylon) into solid layers, building up an object. The unsintered powder supports the structure during printing.
- Materials: Nylon, thermoplastic polyurethane (TPU), composites.
- Applications: Functional prototypes, complex geometries, and low-volume production parts.
- Pros: No need for support structures, durable parts, complex designs possible.
- Cons: Expensive, requires powder handling and post-processing.
Fused Deposition Modeling (FDM)
An FDM printer works by expelling a plastic fiber layer-by-layer onto the forming stage. It’s a savvy and fast strategy for delivering actual models. There are a few occasions when FDM can be utilized for practical testing however the innovation is restricted because of parts having generally harsh surface completes and lacking strength. It is a 3D printing innovation that utilizes a cycle called Material Extrusion. Material Extrusion gadgets are accessible and reasonable of all. They work by a cycle where a spool of a fiber of strong thermoplastic material (PLA, ABS, PET) is stacked into the 3D printer. It is then pushed by an engine through a warmed spout, where it liquefies. The printer’s expulsion head at that point moves along explicit directions, keeping the 3D printing material on a form stage where the printer fiber cools and cements, shaping a strong item. When the layer is finished, the printer sets out another layer, until the item is complete. Basic applications for FDM incorporate electrical lodgings, structure and fit testings, jigs and fixtures, and investment casting patterns. The best part about FDM is that it offers the best surface completion in addition to full tone alongside the reality there are different materials accessible for its utilization. A mechanism of the Machine diagram shown in Figure 4 below.
Figure 4: Fused Deposition Modeling Additive Manufacturing Diagram.
- How it works: FDM/FFF printers extrude thermoplastic filament through a heated nozzle, layer by layer, to build up a 3D object.
- Materials: Common materials include PLA, ABS, PETG, and more advanced filaments like carbon fiber-reinforced composites.
- Applications: Prototyping, hobbyist projects, and functional parts.
- Pros: Affordable, easy to use, wide material availability.
- Cons: Lower resolution and surface finish compared to other technologies.
Digital Light Process (DLP)
DLP has quicker print times than SLA in light of the fact that each layer is uncovered at the same time, rather than following the cross-part of a zone with the purpose of a laser. Primarily uses photopolymer resins as its material. These resins are liquid substances that harden when exposed to a light source. A mechanism of the Machine diagram shown in Figure 5 below.
Figure 5: Digital Light Process Additive Manufacturing Diagram.
- How it works: Similar to SLA, DLP uses a digital light projector to flash an entire layer of an object at once, curing the resin quickly.
- Materials: Photopolymer resins.
- Applications: Similar to SLA but often faster due to entire layers being cured at once.
- Pros: High resolution, smooth surfaces, faster than SLA.
- Cons: Limited build size requires post-processing.
Multi Jet Fusion (MJF)
Multi Jet Fusion (MJF) is a 3D printing technology that builds parts layer by layer using powdered material, typically nylon. It works by spreading a thin layer of powder across a build platform, then selectively applying a fusing agent and a detailing agent using a print head. Infrared lamps heat the areas where the fusing agent is applied, causing the powder to solidify, while the detailing agent ensures sharp edges and fine details. This process repeats until the entire part is formed, followed by cooling and post-processing to remove excess powder. MJF is known for producing strong, detailed, and functional parts, ideal for prototyping and low-volume production. A mechanism of the Machine diagram shown in Figure 6 below.
Figure 6: Multi Jet Fusion Additive Manufacturing Diagram.
- How it works: MJF uses inkjet arrays to selectively apply fusing agents onto a powder bed, which is then fused by heat to form a layer. The process repeats layer by layer.
- Materials: Mainly nylon (PA12, PA11), TPU.
- Applications: Functional prototypes, end-use parts, complex geometries.
- Pros: High detail, excellent mechanical properties, faster than SLS.
- Cons: Expensive, primarily limited to nylon-based materials.
PolyJet
PolyJet 3D printing works by jetting layers of liquid photopolymer onto a build platform, which are then instantly cured by UV light. Multiple print heads move across the platform, depositing tiny droplets of material in precise patterns to build the object layer by layer. The technology allows for the use of multiple materials and colors in a single print, enabling the creation of complex, multi-material parts with smooth surfaces and high detail. A mechanism of the Machine diagram shown in Figure 7 below.
Figure 7: Polyjet Additive Manufacturing Diagram.
- How it works: PolyJet printers jet layers of liquid photopolymer onto a build tray and cure them with UV light. The process repeats layer by layer.
- Materials: Multiple photopolymers that can be combined to create multi-material parts.
- Applications: Prototyping, medical models, complex multi-material parts.
- Pros: High resolution, smooth surfaces, multi-material printing.
- Cons: Expensive, parts may be brittle, requires support removal.
Direct Metal Laser Sintering (DLMS)
Direct Metal Laser Sintering (DMLS) is a 3D printing technology that creates metal parts by fusing powdered metal layer by layer using a high-powered laser. The process begins with a thin layer of metal powder spread across the build platform. A laser then selectively melts the powder in specific areas according to the design, solidifying the layer. This is repeated layer by layer until the entire part is formed. After printing, the part may require heat treatment and post-processing to achieve the desired properties and surface finish. There is no specific diagram for the machine as it’s a complex machine and required to be designed based on the application requirements. For example, if the machine is meant to manufacture boats, specifications required for that application need to be considered when building the machine.
- How it works: Both DMLS and SLM use lasers to melt and fuse metallic powder into solid parts, layer by layer.
- Materials: Metals like titanium, aluminum, stainless steel, and superalloys.
- Applications: Aerospace, medical implants, complex metal parts.
- Pros: Strong, functional metal parts with complex geometries.
- Cons: Very expensive, requires specialized post-processing.
Electron Beam Melting (EBM)
Electron Beam Melting (EBM) is a 3D printing technology that uses an electron beam to melt and fuse layers of metal powder in a vacuum environment. The process starts by spreading a thin layer of metal powder on the build platform. An electron beam then selectively melts the powder according to the digital design, fusing it into a solid layer. This is repeated layer by layer until the entire part is built. The vacuum environment ensures high purity and prevents oxidation. After printing, the part may require post-processing, such as machining or heat treatment. A mechanism of the Machine diagram shown in Figure 8 below.
Figure 8: Electron Beam Melting Additive Manufacturing Diagram.
- How it works: EBM uses an electron beam to melt metal powder layer by layer in a vacuum, building a solid metal part.
- Materials: Titanium and other high-performance metals.
- Applications: Aerospace, medical implants, high-strength metal parts.
- Pros: High-performance metal parts, good mechanical properties.
- Cons: Expensive, limited to specific metals, slower than laser-based methods.